鎳基合金718成分性能
鎳基高溫合金哈氏合金系列材料生產(chǎn)供應商廠家-禎賦(上海)實業(yè)
對應牌號

Incone1718化學成分
C≤0.08 Mn≤0.35 Si≤0.015 P≤0.35 S≤0.015 Cr17~21 Ni50~55 Mo2.8~3.3 Cu≤0.3 Ti0.65~1.15 Al0.2~0.8 Fe余量 Nb4.75~5.5 B≤0.006
物理性能:
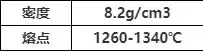
性能

鎳基高溫合金Incone1718因具有優(yōu)良的性能而廣泛應用于航空航天領域,但是起強化作用的強化 合金元素以高硬度化合物形式存在,如TiC、NbC等相間硬質(zhì)點,導致其切削加工性差,被定義為難 加工材料。通過建立Inconel718的多尺度有限元模型,并加入含有cohesive單元的脆性相顆粒進 行切削仿真,深入研究切削Incone1718過程中脆性相對鋸齒形切屑形態(tài)和切削力的影響規(guī)律。結 果表明:通過仿真結果與實驗結果的對比分析,所建立的多尺度有限元模型與普通仿真結果相比, 切屑形態(tài)、切削力等均與實驗結果更加接近,表明所建立的多尺度模型能夠更好的反映Inconel718 的切削過程。
鎳基高溫合金Ineonel718具有良好的抗疲勞、抗 蠕變、抗氧化、耐腐蝕性能,在航空航天領域得到了廣 泛的應用。但是由于鎳基高溫合金是一種典型的難加 工材料,切削過程中存在切削溫度高、塑性變形大等問 題導致其切削加工性很差。目前對于高速切削鎳基高 溫合金Inconel718的研究主要有實驗和有限元模擬兩 種方法。雖然通過實驗研究切削機理是一種可靠的方 法,但高速切削實驗條件復雜,并且很難在切削過程中 準確獲得切削溫度、應力、應變等數(shù)據(jù)…。而有限元 分析方法以其節(jié)省實驗成本、能夠獲得實驗難以測量 的數(shù)據(jù)、結果表示直觀可靠等優(yōu)點在研究金屬切削領 域得到許多學者的青睞。
1973年,美國伊利諾斯大學的B.E.Klameck最先 將有限元技術引入切削過程建模 J,他運用三維有限 元模型分析了切屑形成的最初階段,同時系統(tǒng)地介紹了 金屬切削中切屑形成的原理。1980年,美國北卡羅來那 州立大學的M.R.Lajczok l3 在他的博士學位論文中將 有限元方法應用于切削加工中的主要問題研究,初步分 析了切削工藝。J.S.Strenkowski和J.T.Carroll 在 1985年提出了一個簡化的正交切削模型,對平面應變情況使用廠修正的拉格朗日剛度方程。特別是采用了 新的基于等效塑性應變的切屑分離準則。
美國克里弗 蘭州立大學的T.Ozel(2000) 等利用有限元仿真技 術得到了r件的應變、應變率和溫度等參數(shù)并依據(jù) 這些參數(shù)得到r工件的流動應力公式;他還得到了 刀屑接觸面的剪應力,并依據(jù)剪應力得到了摩擦系 數(shù)的表達式。美同普札大學機械T程學院的 Y.G.Tian 等建立了帶有刀具網(wǎng)角的直角切削模 型,并使用了通用有限元求解器ABAQus/Explicit@ 運算,得到的切削力各分量與實驗結果吻合得較好。 山東大學的唐志濤、劉戰(zhàn)強 。等建立了基于有限變 形理論、虛功原理和更新的托格朗日公式的熱一彈 塑性本構方程,導出了熱一彈塑性大變形耦合控制 方程,對正交切削航空鋁合金的切屑形態(tài)、切削力、 切削溫度以及應力場和應變場等物理場的分布進行 了有效預測。
通過以上文獻可以發(fā)現(xiàn)當前對仿真切削In— conel718的研究存在缺陷:切削Inconel718時存在兩 種材料失效機制,脆性相顆粒失效為脆性失效,基體鎳 基屬于塑性失效,以往的仿真模型將Inconel718看成 為均一材料賦予其材料屬性而忽略脆性顆粒。 本文基于多尺度仿真思想,建立了含有脆性相 顆粒的高速切削Inconel718模型,通過仿真與實驗 結果對比驗證模型可靠性。并進一步分析脆性相顆 粒對切削力以及鋸齒形切屑的影響規(guī)律,為進一步 通過多尺度仿真研究切削Inconel 71 8切削機理提供 基礎.
有限元建模及關鍵技術
1.1 材料本構方程的建立 本文采用的材料本構模型是基于分離式霍普金森 桿的高速變形試驗獲得本構參數(shù)的Johnson—Cook本 構模型:模型具體形式如式(1)所示。
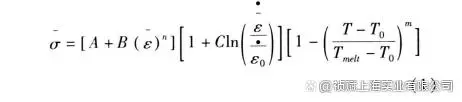
式中; 為等效靼性應力,MPa; 為等效塑性應變; 為等效塑性應變率s~; 。為參考應變率,s~;A為材 料初始屈服應力,MPa;B為硬化模量,MPa;C為應變 率依賴系數(shù)I『I為加工硬化指數(shù);” 為熱軟化系數(shù);T 為材料動態(tài)溫度, ; 為室溫,cIC; 為材料熔化 溫度,℃
通過Hopkinson 桿實驗,獲得IIlconel718的 Johnson—Cook模型各個參數(shù)值女¨表1所 :.
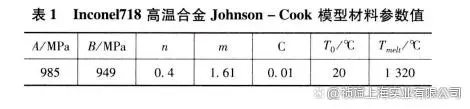
1.2脆性相顆粒建模 Inconel718脆性相顆粒材料主要是 FiC和NbC,璉 本物理參數(shù)如表2所示 。 為了減少計算時間,采H{ 精度偏移的劃分力 式, 在刀具與T件接觸的 域劃分較密的 格,1 件毖體 其他不參與切削的區(qū)域劃分較稀疏的網(wǎng)格 .約束1-件 基體底部沿Y方向的自由度及T件左彳 兩邊節(jié) -上的 方向上的自Fh度。刀具為剛體,限制存) 方向的自 由度,在參考點一I二施加向左的速度。多J 度正交切削 有限元模型如圖1所示。
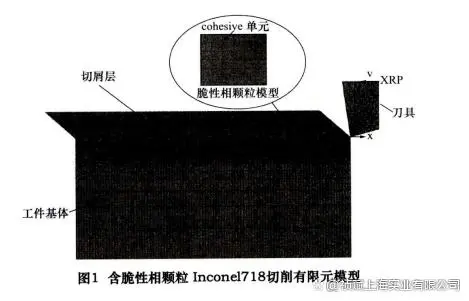
2. 高速切削Inconel718實驗 機床:XK714D型i坐標軸立式數(shù)控銑床。 刀具:整體式涂層硬質(zhì)合金平又 銑刀 、 1一件材料:lnconel718高溫合金塊料,J 寸為70 mill×20 mill×20 lnm。 切削力測量工具:Kistler 9257B切削力測試儀 Inconel718微觀金相組織如罔2所示,其微觀顆 粒隨機分布,彤狀為橢圓形,尺寸在2~20 n 之間.、?
3 結果與分析
3.1切削力 為了研究脆性相對切削力的影響,采用相同的切 削條件(刀具前角 。=6。,進給量廠=0.15 mm/r,切削 速度 =35 m/min)得到瞬態(tài)切削力仿真值與實驗值 的對比圖,如圖3所示;得到切削力波動的對比如圖4 所示。
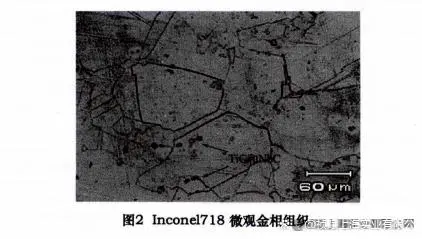
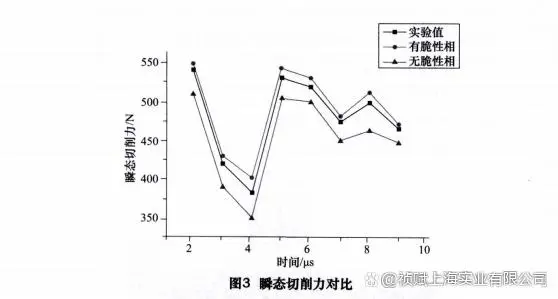
由圖3、圖4可以看出,當切削過程達到穩(wěn)定狀態(tài) 時切削力會呈現(xiàn)有規(guī)律的波動,但是無脆性相模型所 得瞬態(tài)切削力的波動較為平穩(wěn),變化率較小,而加入脆 性相的模型所得瞬態(tài)切削力的波動幅度較大,且力的 大小與波動趨勢與實驗結果更加接近。硬脆相的加入 會引起刀具與工件摩擦增大,切削熱增加,減少了切削 變形的時間,進而導致切削過程不穩(wěn)定,切屑形成過程 中的應變率增大,有利于剪切局部化的發(fā)生。
圖5是采用相同的切削條件(刀具前角 =6。, 進給量/=0.15 mm/r,切削速度分別取 :30 m/min; 2=35 m/min; 3=40 m/min; 4=45 nv'min)得到的平 均主切削力的對比圖。 由圖5可知,仿真結果與實驗結果大體吻合,平均 主切削力都是隨著切削速度的提高而減小。與實驗值 對比,有脆性相模型仿真值較大,而無脆性相仿真值偏小,但是有脆性相顆粒模型的仿真值更加接近實驗值, 這是因為顆粒是脆性材料,刀具經(jīng)過顆粒所在區(qū)域時, 顆粒本身受力無塑性變形,顆粒與刀具之間屬于“硬 接觸”,這種間接的接觸性質(zhì)對刀具產(chǎn)生力的作用導 致進給力增大,進而使得切削力變大。
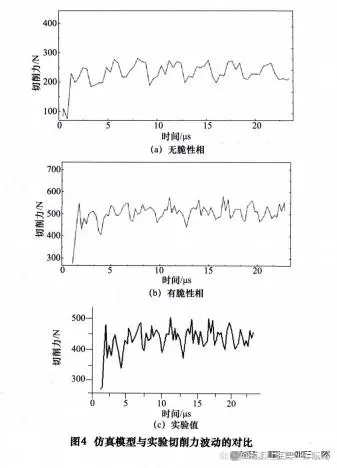

3.2鋸齒屑形成 圖6是在相同切削條件(切削速度 =60 m/rain) 仿真切屑和實驗切屑形態(tài)對比圖。南岡可以看出,與 不加脆性相顆粒相比,加入脆性相顆粒之后得到的切 屑形態(tài)變得不規(guī)則,切屑齒高和齒距與實驗結果更加 符合。
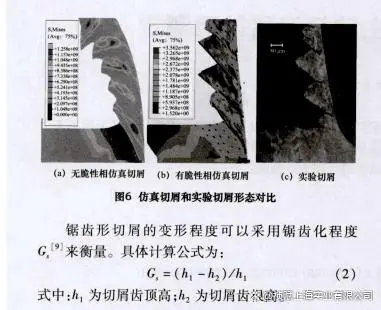
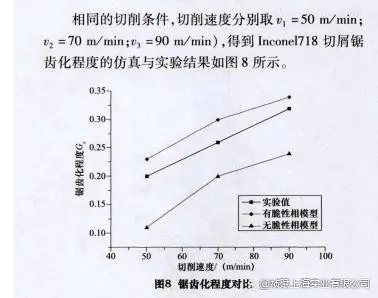
由圖可以看m,仿真模型得到的鋸齒化程度與實驗 結果大體一致,鋸齒化程度隨切削速度的提高而增大。 有脆性相的模型所得的鋸齒化程度稍微偏大,這是因為 加入脆性相顆粒后,導致刀具與工件的摩擦加劇,使得 在切削過程中溫度增高,促進了熱軟化效應,第一變形 區(qū)處于絕熱剪切失穩(wěn)狀態(tài),材料的剪切抗力急劇減小使 得剪切區(qū)絕熱剪切變形加劇,更有利于鋸齒形切屑的形成,因此加入脆性相后鋸齒化程度增大,但與不加脆性 相模型相比更加符合實驗結果。又因為鎳基合金中脆 性相顆粒的大小不等且分布不均勻,具有隨機性,最終 導致加入脆性相后切屑上相鄰的齒高與齒寬不等,切屑 形態(tài)變得不規(guī)則,更加接近實驗結果。