廢舊鋰電池回收處理設(shè)備電池極片材料的回收方法
隨著國(guó)家對(duì)電動(dòng)汽車(chē)的大力推廣,未來(lái)將有大量動(dòng)力鋰電池面臨報(bào)廢的問(wèn)題,根據(jù)中國(guó)汽車(chē)技術(shù)研究中心的預(yù)計(jì),我國(guó)廢棄電池的回收率不足2%,而廢舊鋰離子電池中含有大量可利用的資源,例如鋁,銅等有價(jià)金屬以及石墨,正極材料等;如果這些廢舊鋰電池處理不當(dāng),將造成很大的資源浪費(fèi)和環(huán)境污染。
目前,鋰離子電池中的主要有價(jià)回收物質(zhì)為銅、鋁、正極粉料及負(fù)極粉料,并且90%以上有價(jià)回收物質(zhì)都在鋰電池正負(fù)極片上,其中鋰電池正極片為鋁箔涂敷正極材料,鋰電池負(fù)極片為銅箔涂敷負(fù)極材料。如何提高銅、鋁、正極材料及負(fù)極材料回收率及純度,是急需解決的問(wèn)題。目前大多采用化學(xué)方法提高回收物料純度,但是這些方法使用大量的有機(jī)試劑包括酸、萃取劑,會(huì)對(duì)環(huán)境造成二次污染。
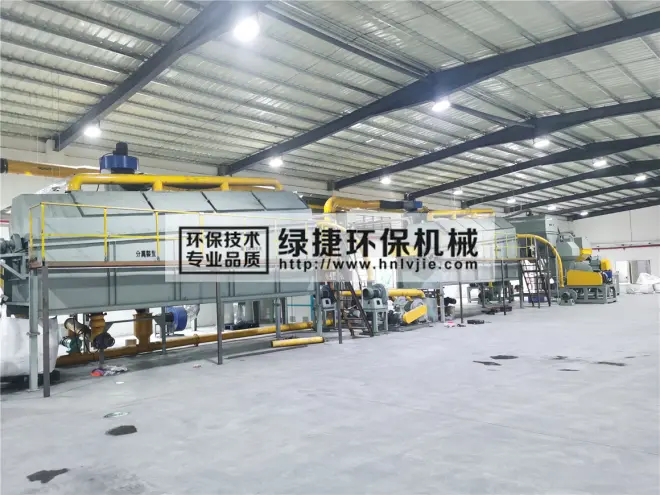
廢舊鋰電池回收處理設(shè)備一種工藝簡(jiǎn)單、低能耗的鋰離子電池極片材料的回收方法包括:將極片粉擠壓,篩分,得到篩上的餅狀集流體金屬顆粒和篩下的電極材料粉體;極片粉為將正極片或負(fù)極片粉碎后得到的粉體。包括以下步驟:
1)將回收的鋰離子電池放電、排出電解液,然后拆解得到負(fù)極極片,再將得到的銅極極片粉碎得到目數(shù)為50~100目的負(fù)極極片粉;
2)通過(guò)先風(fēng)選,然后再篩選的方式從步驟1)所得的負(fù)極極片粉中分離出大約95%(占正極材料細(xì)粉的質(zhì)量百分比)金屬銅基材,剩余的為含銅大約5%(占負(fù)極材料細(xì)粉的質(zhì)量百分比)的負(fù)極材料細(xì)粉;
3)將負(fù)極材料細(xì)粉采用300目的輥磨機(jī)輥磨,然后采用300目的超聲振動(dòng)篩篩分,得到篩上的餅狀的集流體金屬銅顆粒a和篩下的負(fù)極材料粉體a;

4)將步驟2)得到負(fù)極材料粉體a采用500目的輥磨機(jī)輥磨,再采用500目的超聲振動(dòng)篩篩分,得到集流體金屬銅顆粒b和純度更高的負(fù)極材料粉體b;
5)將步驟3)得到的負(fù)極材料粉體b采用800目的輥磨機(jī)輥磨,再采用800目的超聲振動(dòng)篩篩分,得到集流體金屬銅顆粒c和純度更高的負(fù)極材料粉體;其中負(fù)極材料粉體純度能達(dá)到99%以上;
6)將步驟3)得到的銅顆粒a、步驟4)得到的銅顆粒b和步驟5)得到的銅顆粒c混合。
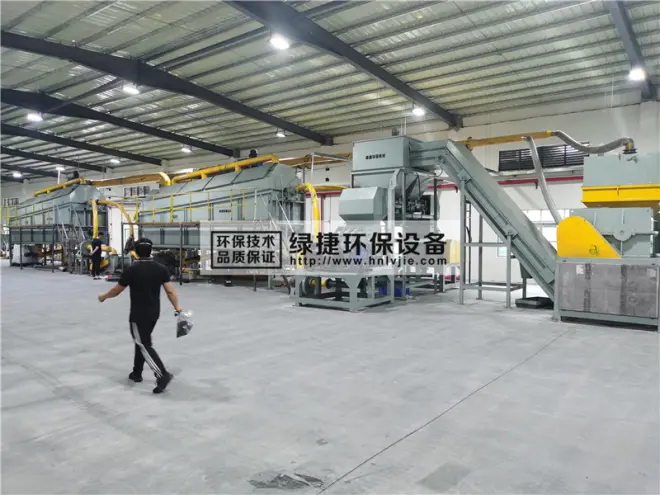
鋰離子電池極片材料的回收方法,工藝簡(jiǎn)單,由于極片在粉碎的過(guò)程中,極片材料容易從集流體體上脫落變成粉狀,而集流體體碎片則容易團(tuán)成球狀或塊狀的顆粒;利用金屬鋁和銅延展性良好的特點(diǎn),將粉碎后的極片細(xì)粉擠壓,極片粉中的鋁顆粒或銅顆粒會(huì)被擠壓為餅狀,而其他顆粒進(jìn)一步被粉碎為更細(xì)小的顆粒,再通過(guò)篩分將餅狀的鋁顆?;蜚~顆粒與其他顆粒分開(kāi),既提高了得到的電極材料粉體的純度,又提高了鋁或銅的回收效率,并且整個(gè)過(guò)程不需要任何化學(xué)試劑,不產(chǎn)生二次污染。
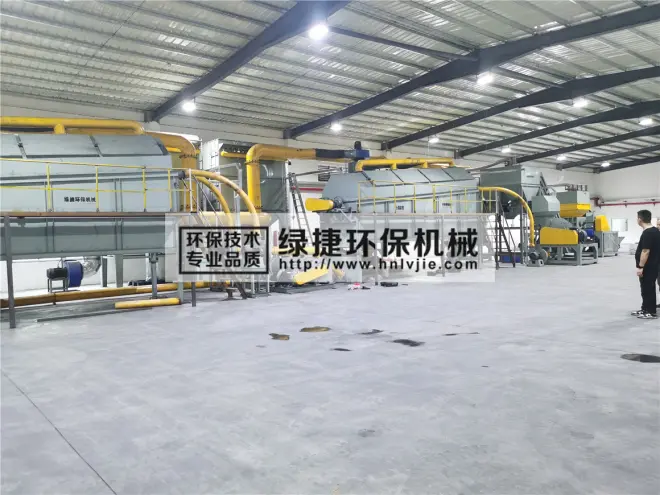
先將極片粉進(jìn)行分選去除大粒徑集流體碎片顆粒,再將剩余電極材料細(xì)粉進(jìn)行擠壓。分選可以采用篩選,或先風(fēng)選、再篩選的方式。采用先風(fēng)選、再篩選的方式可以從極片粉中分離出大約95%(質(zhì)量百分比)集流體,但仍有約占剩余電極材料細(xì)粉總質(zhì)量5%的集流體碎片顆?;烊胝?負(fù)極極片粉里。
極片粉的粒徑小于5mm,極片粉的粒徑為50~100目。分選為先將極片粉進(jìn)行風(fēng)選,然后篩選。擠壓為輥壓或輥磨。輥壓采用輥壓機(jī)。輥磨采用輥磨機(jī)。輥磨機(jī)的目數(shù)和篩分時(shí)采用篩網(wǎng)的目數(shù)相同。篩分為超聲振動(dòng)篩篩分。
鋰離子電池極片材料的回收方法,還包括:將得到的極片粉重復(fù)進(jìn)行擠壓、篩分。多次進(jìn)行擠壓、篩分能夠進(jìn)一步提高電極材料粉體的純度,并且能夠提高鋁或銅的回收率。擠壓采用輥磨機(jī),重復(fù)進(jìn)行輥磨、篩分時(shí),輥磨和篩分采用的目數(shù)小于前一次采用的目數(shù)。